2022 - ARCH 6605 Architectural 3D Printing, Sasa Zivkovic - Project partnered with Cynthia Kuo
In concrete structures, formwork is essential for strength development and geometry realization. It occupies a large portion of costs in the construction of concrete structures. The formwork reuse rate, however, is low and contributes to construction waste. 3D printing technologies, an additive manufacturing technique, eliminate the use of formwork and allow for mass customization, which can effectively reduce the production cost and improve production efficiency. This research explores the reinforcement strategies and the optimization of overhang and material for 3D printed concrete beams. Limited in tensile and flexural resistance, concrete has the advantages of high compressive strength, low deformation, and remarkable durability.
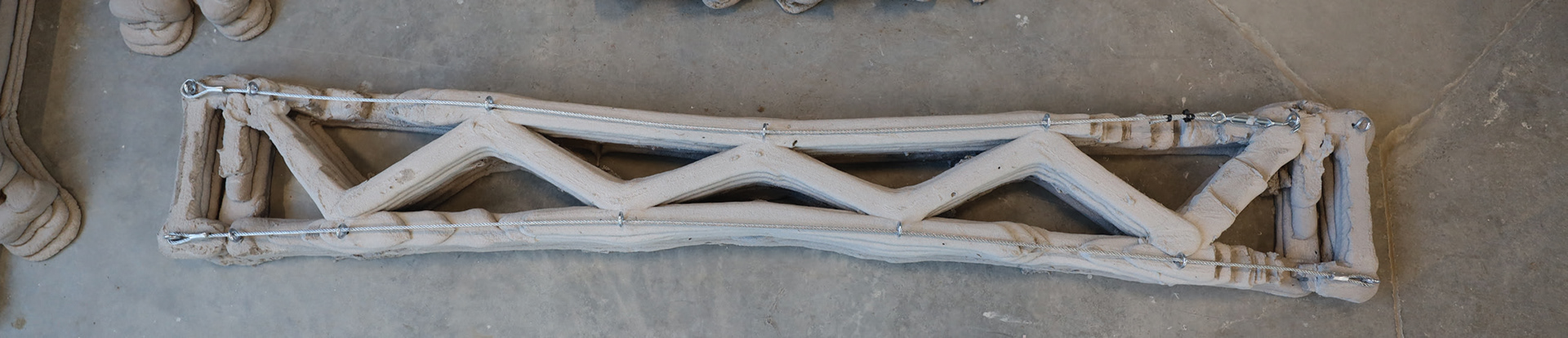
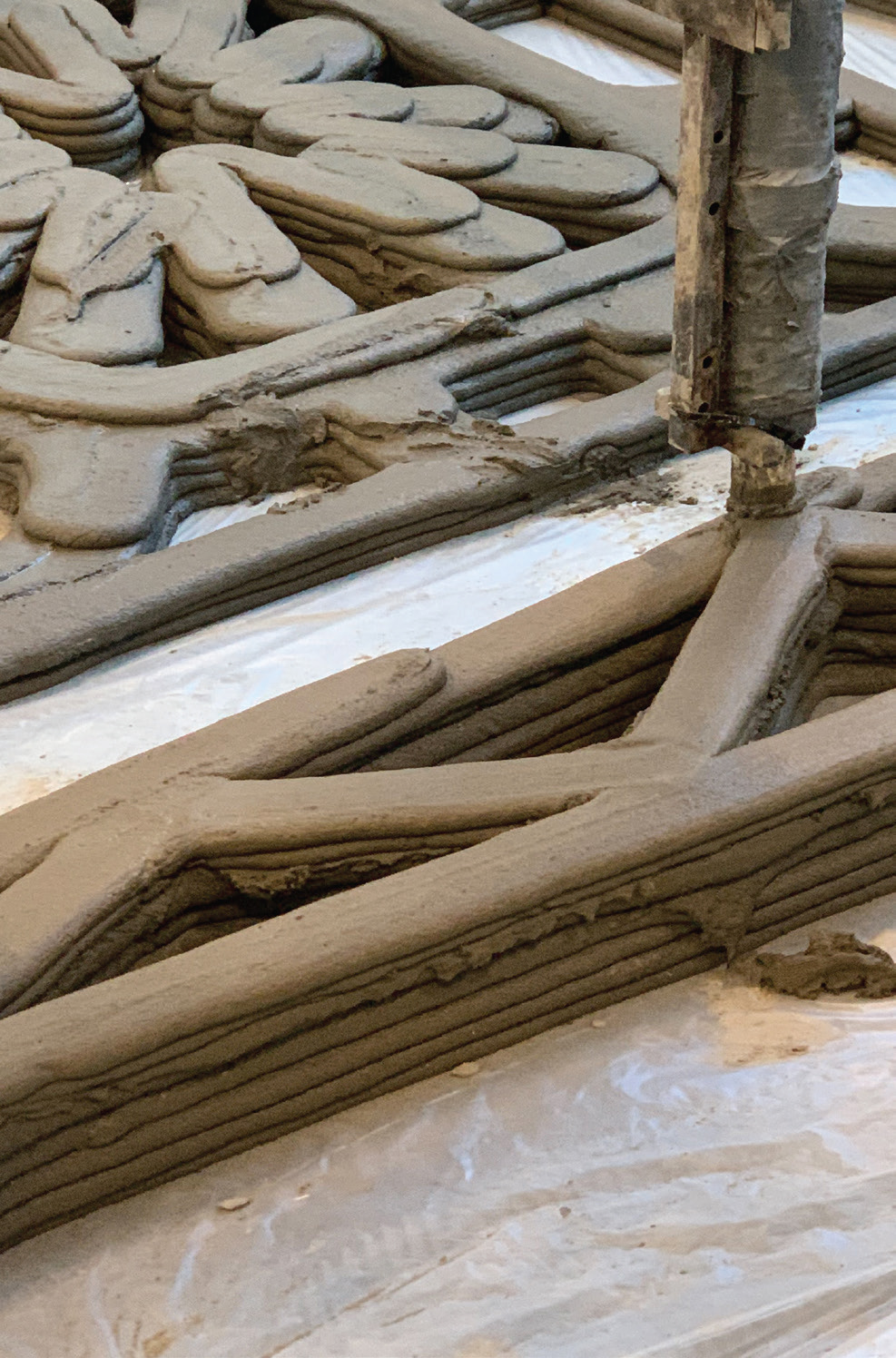
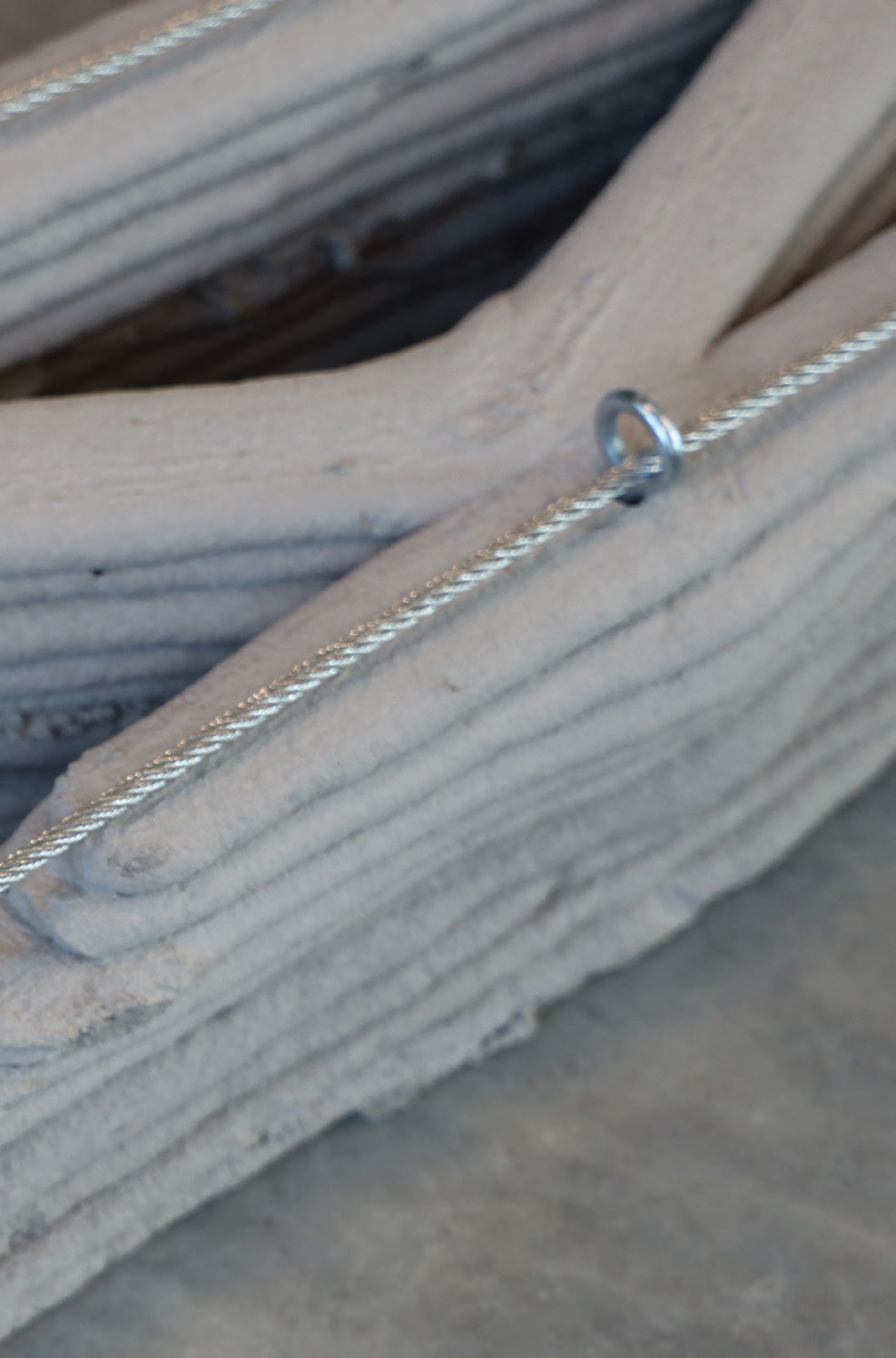
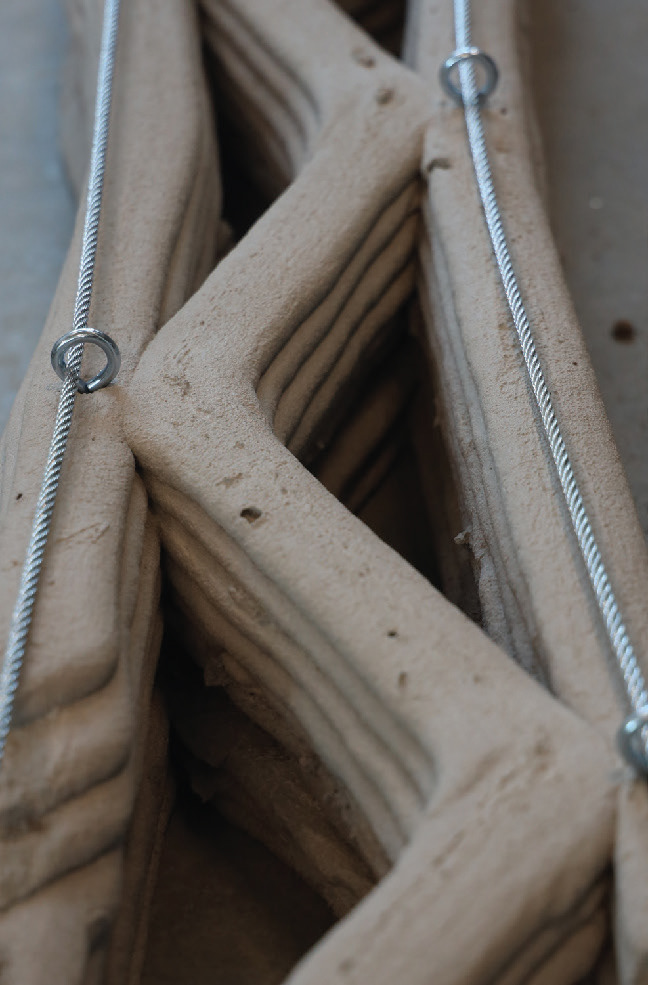
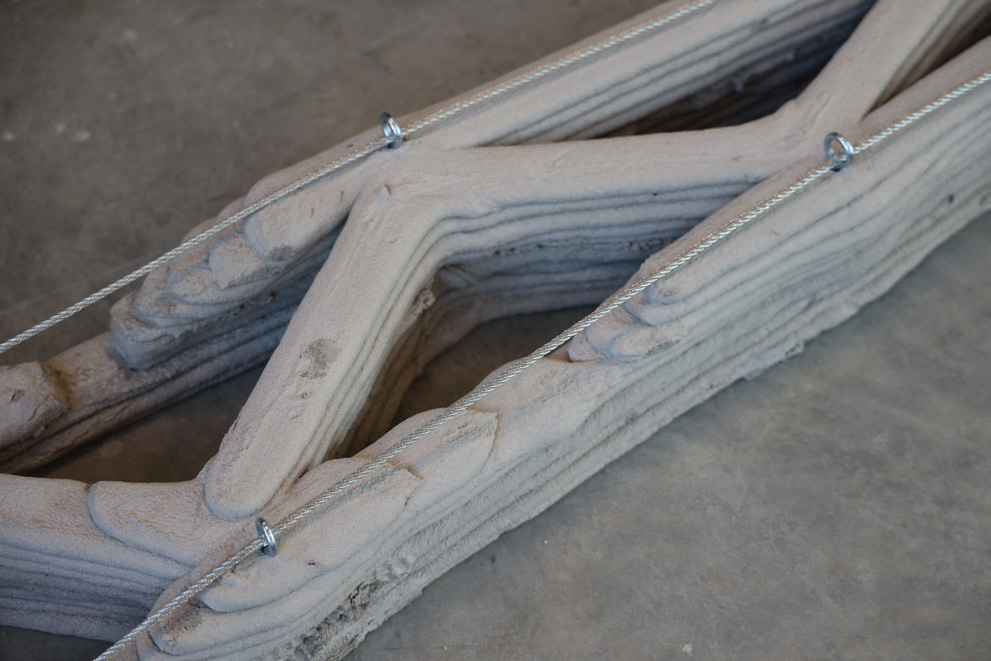
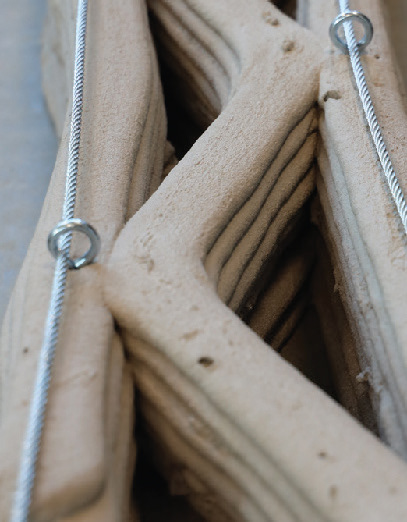
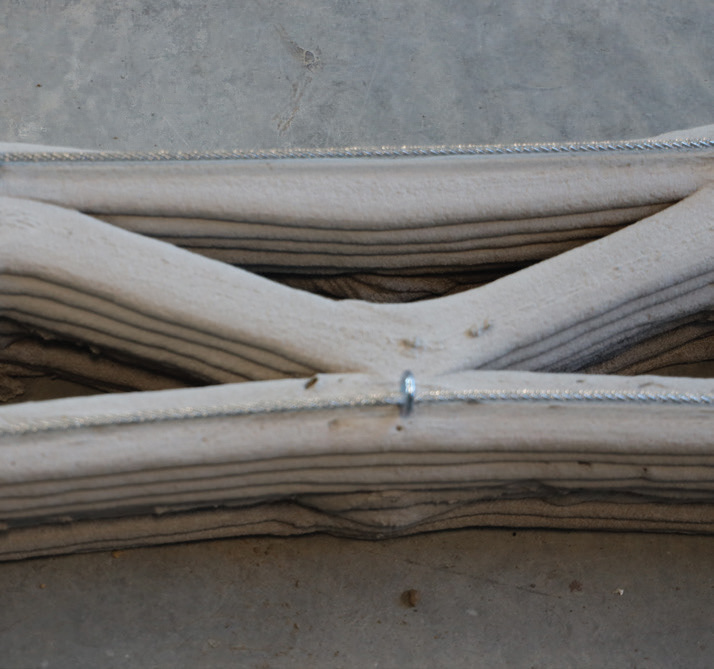
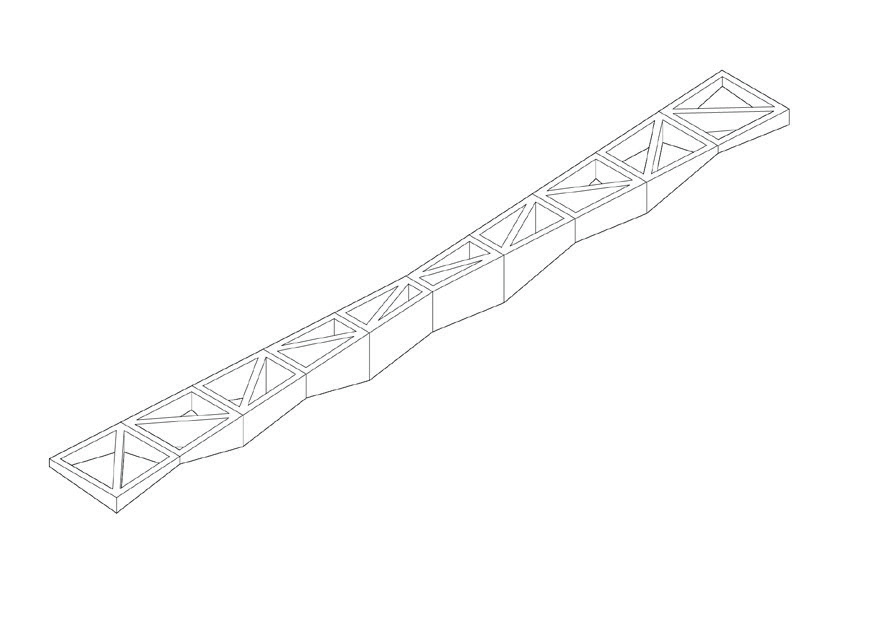
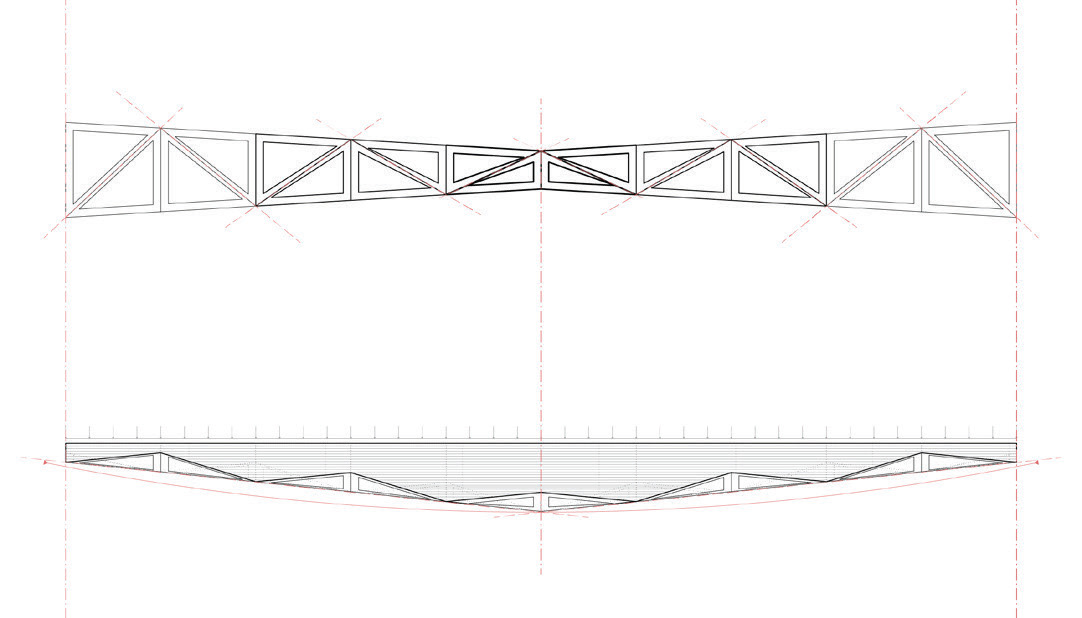
The cross section of the beam profile is optimized according to the stress distribution. More material is distributed in the compressive part, with tighter bracing openings. The width at the center of the beam is decreased in order to reduce the overall weight of the printed concrete.
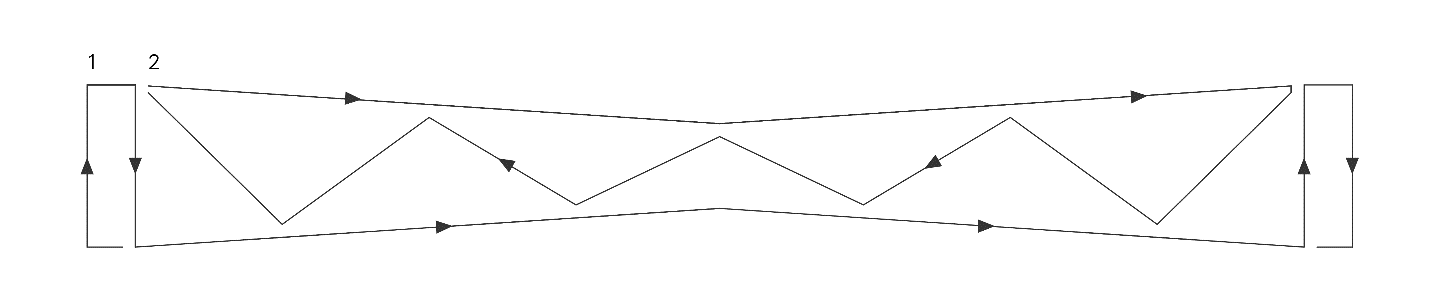
The toolpath is optimized and grouped into two continuous strokes (Figure 1). The first stroke outlines the overall perimeter of the beam. The second stroke completes the perimeter and traces the internal bracings in a zigzag direction. The offset spacing between the two strokes is found to be performing the best at 25mm. 25mm allows concrete to join seamlessly and neatly without overly excessive bulging joints.
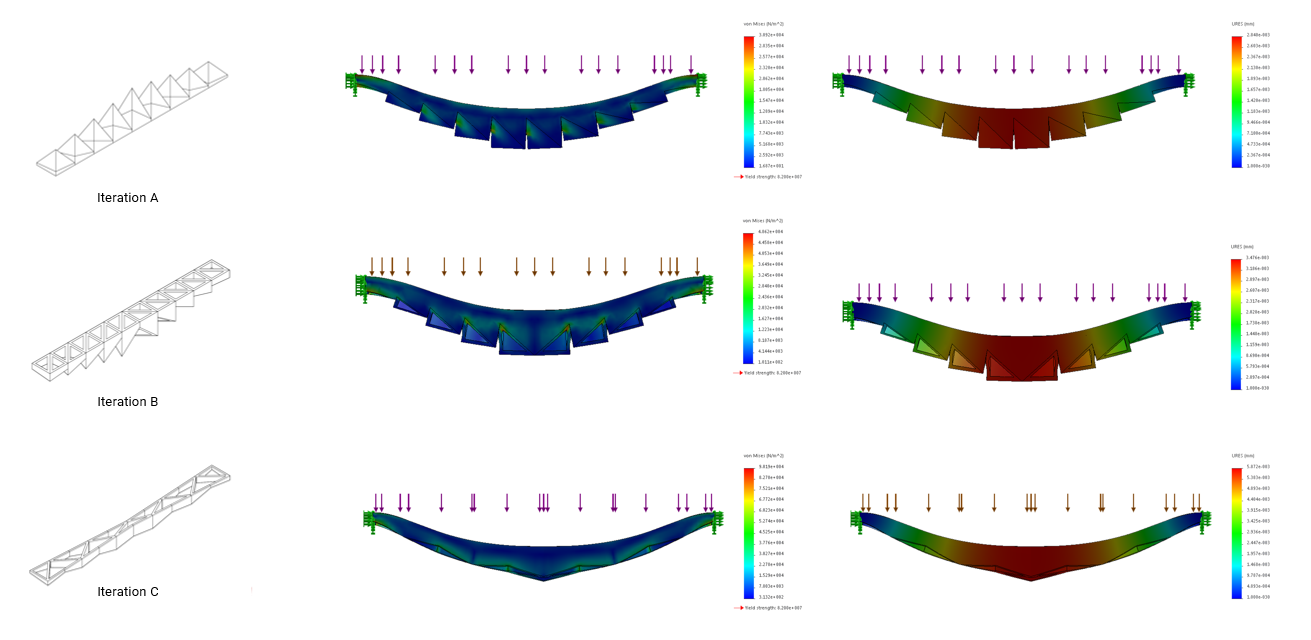
The beam is reoriented upside down during the printing process. The top of the beam lays flat on the ground, and the arching profile faces upward. Toolpath consists of 2 continuous strokes.
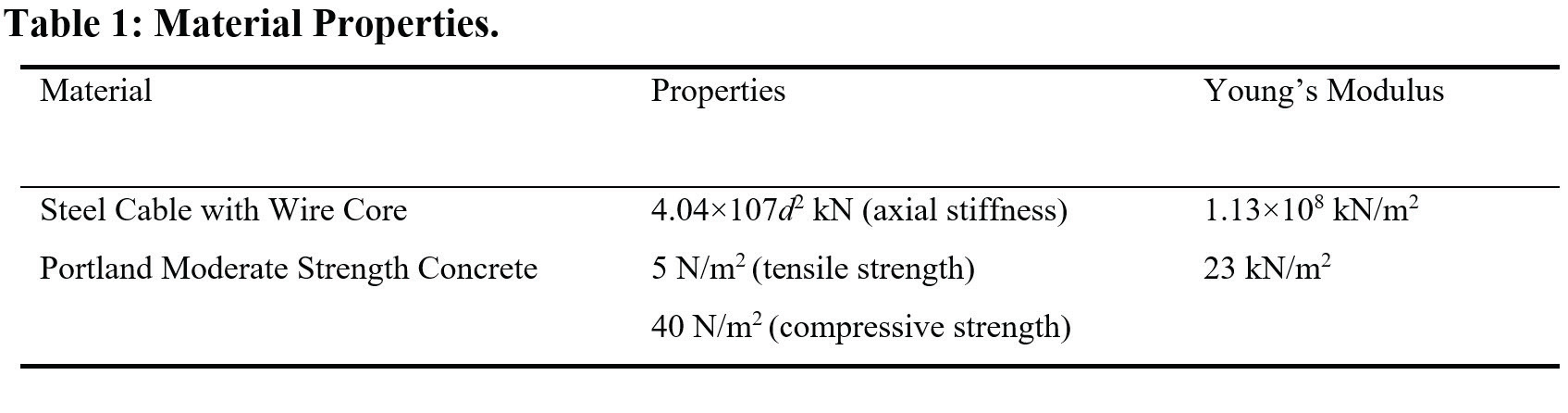
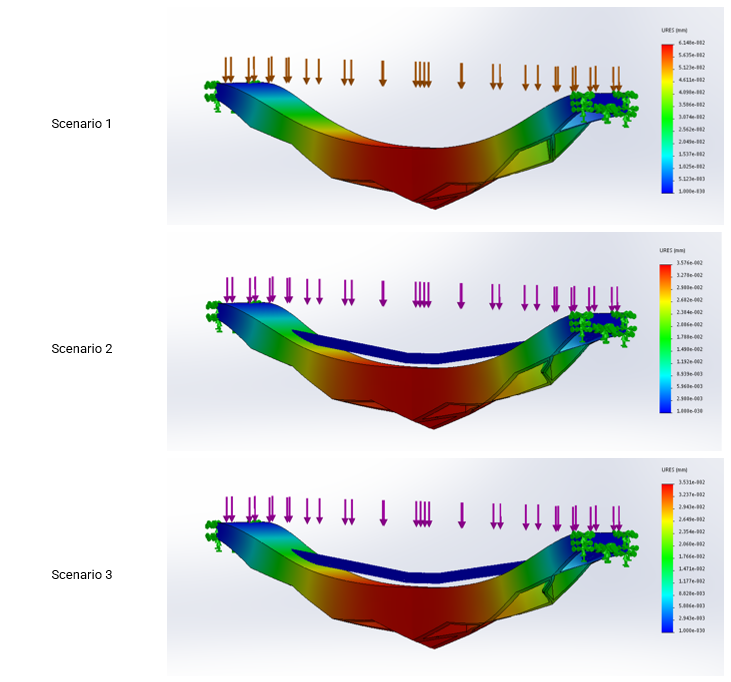